South jersey piano
Supporting the musicians of southern NJ since 2010
Our Services
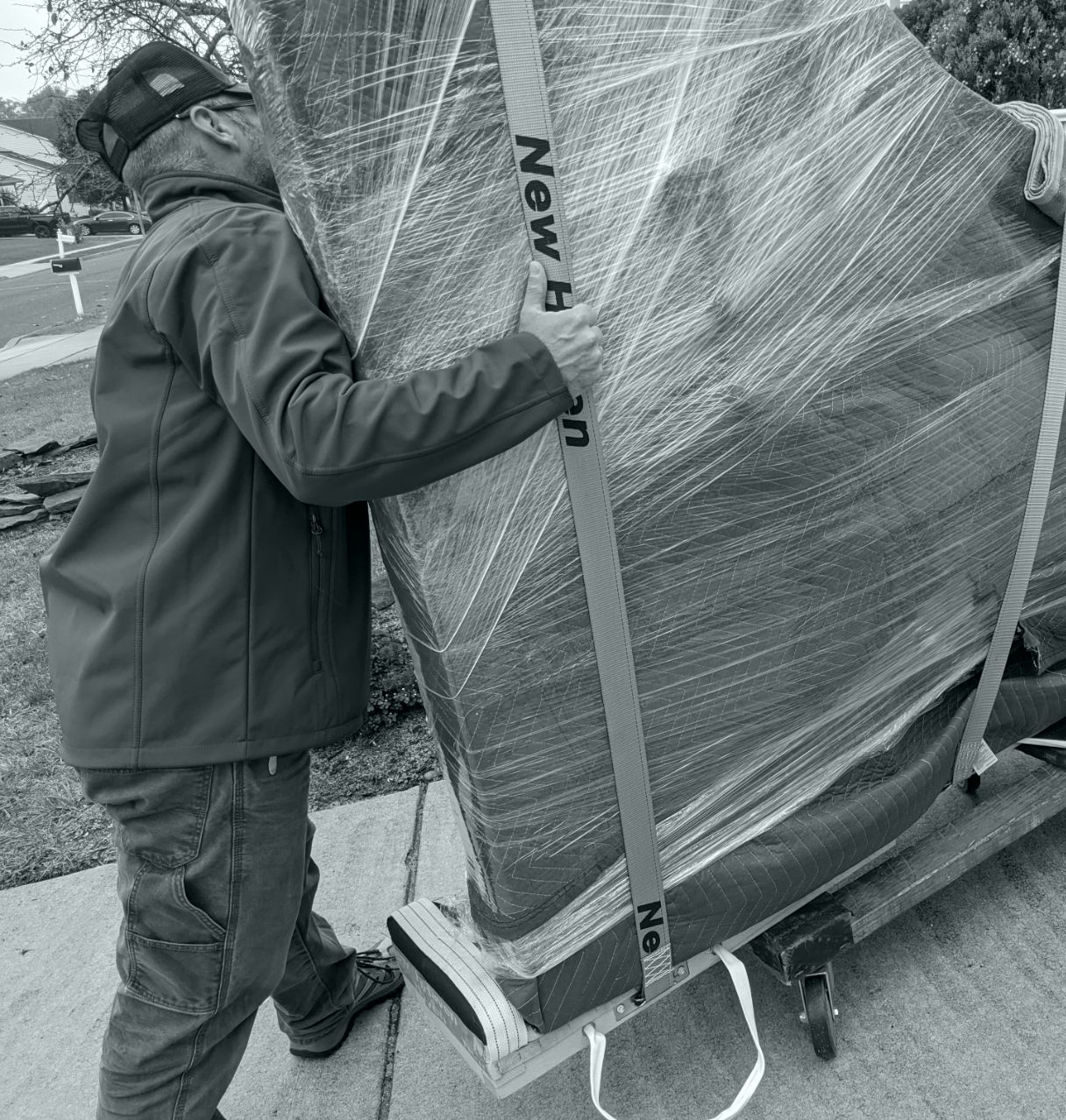
Piano Moving
We offer professional piano moving services for uprights and grands throughout southern NJ and surrounding regions.
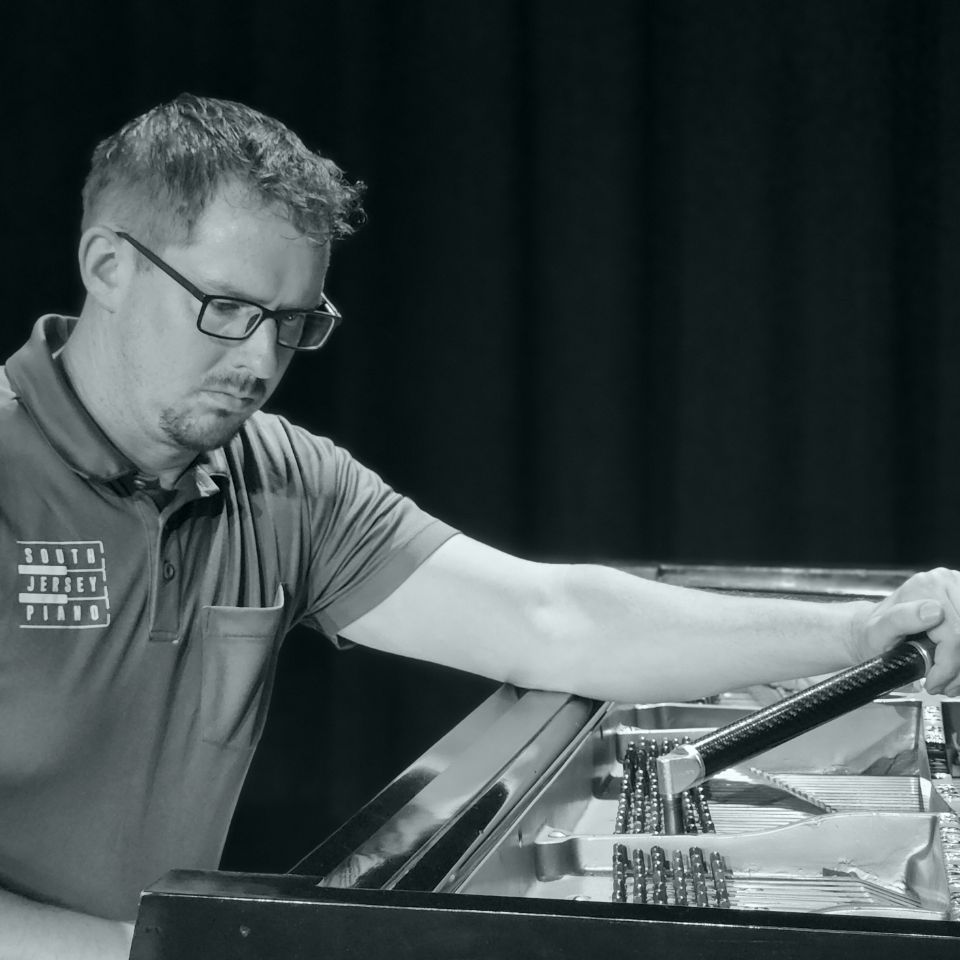
Piano Tuning
The lifeblood of piano maintenance. Most pianos are tuned annually or biannually, more frequently for heavily played or performance venue pianos.
Piano Sales
We have a small selection of used grands and uprights for sale. If you are looking for something specific, we’d be happy to help!
Studio & Rentals
We can provide both short-term event rentals and long-term home rentals of uprights and grands. Our recording studio houses a pristine, immaculately maintained Yamaha C7 semi-concert grand which is also available for rental or studio sessions.
Other services we offer
Piano regulation
We’ll adjust the mechanical action of the piano to give proper touch, response, and control Read more
Piano voicing
We’ll refine the tone quality, attack, sustain, and timbre of your piano Read more
Keytop replacement
Refresh your piano’s look with new key-tops Read more
Piano finish repair
We do on-site and shop repairs, and can refer to other specialists for more complex or unusual jobs Read more
Piano Lifesaver humidity control
We install a humidity control system designed to help your piano last longer and maintain greater tuning stability Read more
Piano appraisal
Get a thoroughly documented report on your piano’s condition and market value Read more
Read more
Highly recommended for those who care about keeping their pianos in tip top shape.
Put your piano in the hands of true musicians and piano experts
With South Jersey Piano, you can be assured that your instrument will sound better than ever and stand the test of time.